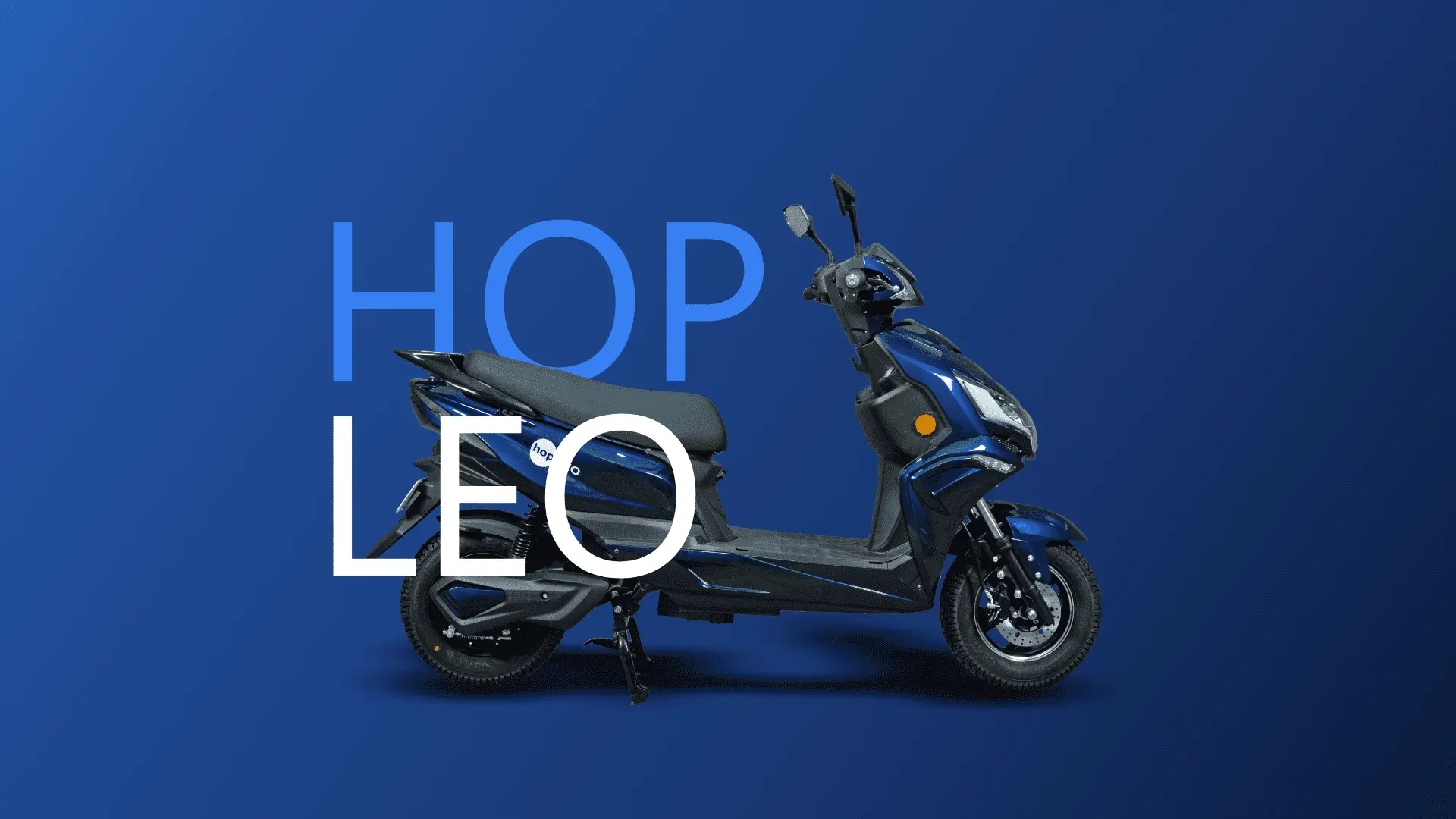
About
Detailed Case Study
.png)
With Grid, Hop Electric has digitalized its Manufacturing, Quality Control, and Dealership Management System (DMS) processes in less than 1.5 months. As a result, HE has accelerated production and distribution for the Indian EVmarket while reducing quality issues by 40%.
Grid has also enhanced Hop’s Manufacturing Planning by 30% with centralized DMS that gives 100% real-time visibility into market demand.
Hop Electric At A Glance
- 200+ Users
- 150+ Dealers
- 10,000+ Vehicles Manufactured
Timeline
How did Grid & Longford Exploration collaboration come about?
Grid and Hop Electric first partnered in March 2021 to:
1. Expedite the growth of Hop’s New Energy Mobility Ecosystem
2. Setup a Dealership Management System for efficient Market Expansion
3. Digitize Quality Assurance Model for smooth nationwide deliveries
.png)
Snapshot
Who’s using Grid @ Hop and how?
.png)
Before Grid
Reliance on legacy and outdated solutions that resulted in:
• Productivity Loss
• Data Mismanagement
• Lack of Visibility in Distribution
Grid combines and makes available all those different functionalities in a single powerful and flexible tool:
MS Excel / Google Sheets
Usage:
• Non-standardized data collected from multiple sources
• Manual collation on Excel by MIS Teams
• Sheets forwarded to Project Heads for final check and commissioning.
Issues:
• Lack of Data Synchronization and Version Control in MS Excel
• Time-consuming and prone to input errors
• Difficulty in Progress Tracking
Standalone Custom built CCMS
Usage: Orders placed by dealers are done via WhatsApp, Phone-calls, etc.
Issues:
• Broken Order Placement channel with Dealers
• Frequent disruptions, delays, and errors
• No Automated Tracking System for Insight and Visibility
• Mismanagement of multiplecommunication channels
Paper Logs
Usage:
• Data Collection along production line on paper
• MIS Team conducts Data Transfer from paper to computer
• Transferred data stored in decentralized Excel sheets
Issues:
• Critically prone to input errors
• Zero standardization of data
• Data misreporting renders new-age tech’s efficiency useless
Operations @ Hop Electric Powered By Grid
Production Readiness Assessment
• Vehicle Assembly Tracking System along the Production Line
• QR code assigned to every component and chassis
Key Benefits
• Standardized Data collection
• Real time view of project status
Post Assembly Vehicle Quality Control
• Digitized quality checklists to ensure manufacturing consistency
• Faultless delivery management system for vehicles
• Automated QC reporting for chassis to ensure proper inspections
Key Benefits
• Reduction in quality complaints
• Zero product recall
• Seamless vehicle delivery
Dealer Registration
• Smooth 4-step Onboarding workflow for new dealers
• Automatic Dealer-Code Assignment and KYC Completion
• Library Creation and Management of legal documents and agreements
Key Benefits
• Single source of truth for zonal dealership network
• Standardization in nationwide dealership set-up and operations
• Centralized dealer database for accurate sales insights
Order Management and Inventory
• End-to-end Purchase Order issue setup for Dealer-to-Hop
• Systematic Vehicle Dispatching by Factory Managers
• Invoice Creation and Tracking
• GRN flow management and QC Ticketing System
• Inventory Tracking across Value chain
Key Benefits
• Dealer-level performance dashboards to track sales targets
• Automated PO and Approval Channel b/w dealers and Zonal Managers
• Smoother logistics planning wrt demand
How Hop Electric uses Grid
.png)
Dealership Management System
• Standardized Onboarding and Operations workflow for new dealerships
• Library Creation and Management of legal documents and agreements
• Automated Purchase Order and Approval Channel b/w Dealers and Zonal Managers
• Customizable dealership performance dashboards and reports
• GRN flow management along with a centralized QC Ticketing system
• Proactive Manufacturing Planning wrt Market Demand
- Step 01: 4-Step Onboarding process with automated dealer-code assignment, KYC completion, and documentation generation.
- Step 02: Creation of Purchase Orders on Grid sent to Zonal Sales Managers for quantity approval.
- Step 03: DMS dashboards provide 100% visibility into dealership sales and targets.
- Step 04: As a result, Manufacturing + Logistics Planning turns increasingly efficient.
.png)
Post Assembly Quality Control
• Real-time recording of Progress and Product Quality.
• Zero data misreporting due to digitized Quality Checklist and Assurance modules.
• User-friendly mobile framework ensures data can be shared from anywhere anytime.
• Automated QC reporting for chassis consistency.
• Hassle-free Vehicle Dispatchment post-inspection
- Step 01: Meticulous inspection using Grid’s digitized checklists with centralized monitoring by QC managers.
- Step 02: Vehicles approved for delivery to zonal dealerships post-inspection.
- Step 03: As a result, quality complaints from dealers were reduced by 40%.
Related case studies
_imresizer.jpg)
Workforce Management with Grid
Grid's no-code workforce management solution was utilized by a utility to address existing concerns in task scheduling, resource allocation, service delivery and more. Read on to find out.
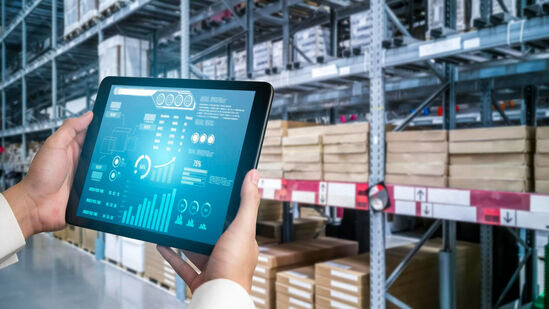
Real-Time Analytics and Custom Reporting for a European Utility
Explore how Grid enabled a leading utility to overcome its data management and warehousing challenges, with a custom reporting engine for greater scalability and real-time monitoring.