In the manufacturing industry, efficient production planning and scheduling are key factors that can significantly impact the success of a business. The ability to effectively plan and schedule production activities can lead to increased productivity, reduced costs, and improved customer satisfaction. This article will explore the basics of production planning and scheduling, the importance of each in manufacturing, strategies for successful implementation, techniques for effective scheduling, integration of production planning and scheduling, and the future of these processes.
Understanding the Basics of Production Planning
Production planning plays a crucial role in the manufacturing industry. It involves the coordination of various resources, such as materials, labor, and equipment, to ensure the timely and efficient production of goods. A well-executed production plan takes into account factors like demand, available resources, and production capacity to create a roadmap for the manufacturing process.
But what exactly does production planning entail? Let's dive deeper into this topic to gain a better understanding.
At its core, production planning aims to balance customer demand and available resources to meet production goals. By analyzing historical sales data, market trends, and customer forecasts, manufacturers can determine the desired production levels and develop a plan that maximizes efficiency and minimizes waste.
Imagine a scenario where a manufacturing company receives a large order for a popular product. Without proper production planning, they might struggle to fulfill the order on time, leading to dissatisfied customers and potential loss of business. However, with an effective production plan in place, the company can ensure that the necessary materials, labor, and equipment are available to meet the demand and deliver the products on schedule.
The Role of Production Planning in Manufacturing
Efficient production planning not only ensures timely delivery of products but also minimizes inventory costs. By accurately forecasting demand and aligning production accordingly, manufacturers can avoid excess inventory that ties up valuable resources and increases carrying costs.
Additionally, it enables manufacturers to respond quickly to changing customer demands, reducing the risk of stockouts or backorders.
When manufacturers have a clear understanding of customer demand, they can plan their production schedules accordingly. This allows them to produce just the right amount of goods, eliminating the need for excessive stockpiling. By avoiding excess inventory, manufacturers can free up warehouse space, reduce the risk of product obsolescence, and save on inventory carrying costs.
Moreover, efficient production planning enables manufacturers to respond swiftly to changes in customer demands. In today's fast-paced market, customer preferences can change rapidly. By having a flexible production plan in place, manufacturers can quickly adjust their production schedules to meet the new demand, ensuring that they don't miss out on potential sales opportunities.
Key Elements of Effective Production Planning
Effective production planning requires careful consideration of several key elements:
1. Accurate Demand Forecasting
Crucial to determine the required production volume. By analyzing historical data and trends, manufacturers can draft precise forecasts that support efficient planning.
Imagine a manufacturing company that produces seasonal products. By analyzing sales data from previous years, they can identify patterns and trends that help them predict the demand for each season accurately. Armed with this information, they can adjust their schedules accordingly, ensuring that they have enough stock to meet the expected demand during peak seasons while avoiding excess inventory during slower periods.
2. Production Capacity Analysis
Understanding the organization's capabilities and limitations allows manufacturers to set realistic production goals and avoid overloading resources.
Let's consider a scenario where a company has limited production capacity due to a shortage of skilled labor. By analyzing their production capacity and identifying the constraints, they can plan their production schedules in a way that maximizes efficiency without overwhelming their resources. This might involve outsourcing certain production tasks or investing in training programs to expand their production capabilities.
3. Effective Communication
Collaboration among different departments, such as sales, production, and procurement, are critical for an optimal supply chain. Clear communication ensures that production plans align with market demands and available resources.
Imagine a situation where the sales department receives a large order from a new customer. Without proper communication with the production department, they might commit to delivering the order within an unrealistic time-frame, leading to potential production delays and customer dissatisfaction.
In conclusion, production planning is a vital process in the manufacturing industry. It helps manufacturers balance customer demand and available resources, ensuring timely delivery of products while minimizing inventory costs. By accurately forecasting demand, analyzing production capacity, and fostering effective communication, manufacturers can develop robust production plans that drive efficiency and success.
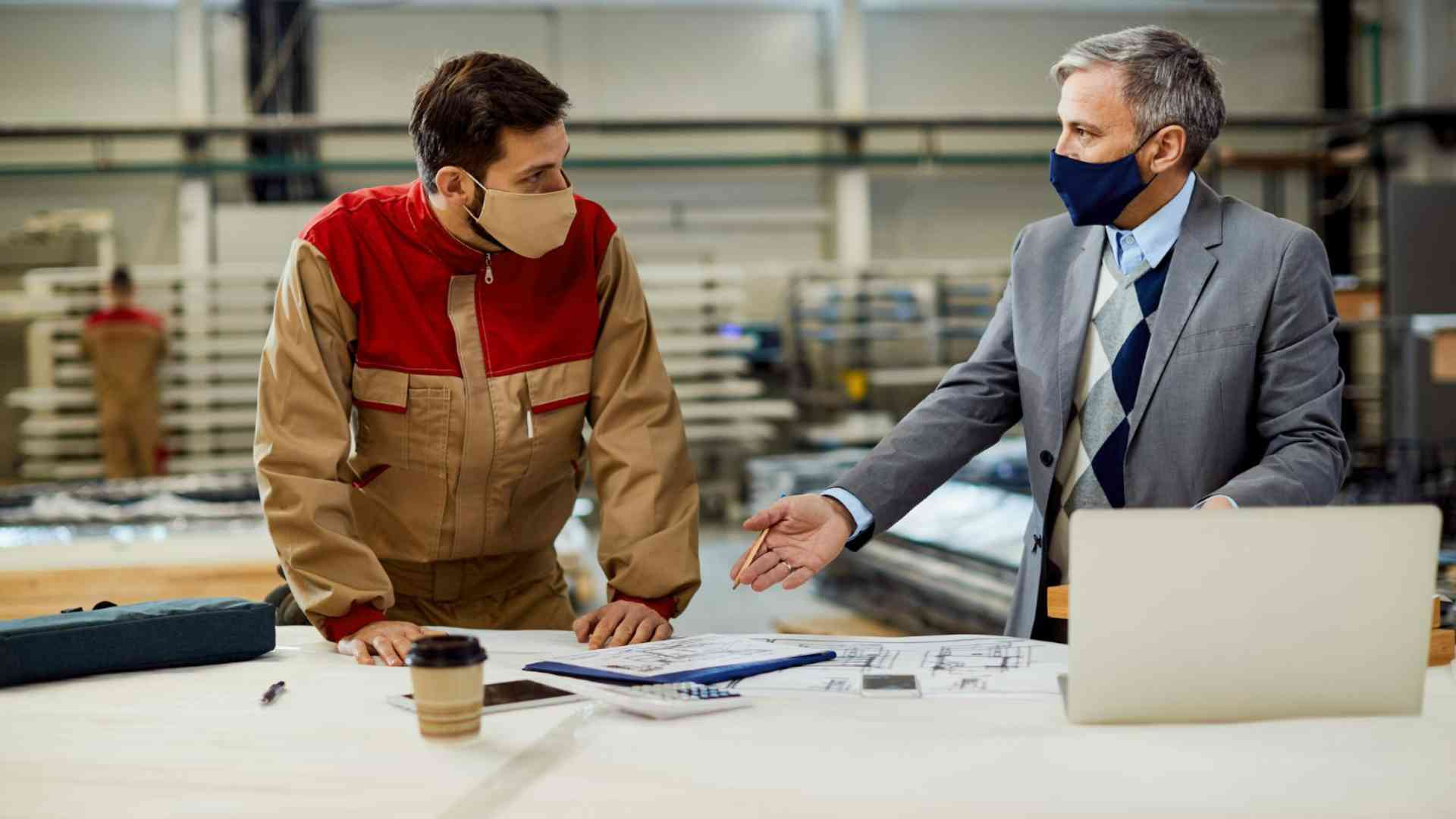
The Importance of Scheduling in Manufacturing
Scheduling is another critical aspect of the manufacturing process that directly impacts productivity and efficiency. Scheduling involves determining the sequence of manufacturing operations and allocating resources to achieve the planned production objectives.
In manufacturing, every minute counts. Efficient scheduling plays a vital role in maximizing productivity. It allows manufacturers to utilize resources effectively, minimize idle time, and reduce production bottlenecks. By sequencing operations strategically, manufacturers can optimize the use of equipment, reduce setup times, and minimize material handling.
How Scheduling Impacts Productivity
Efficient scheduling is like a well-orchestrated symphony. It ensures that each operation flows seamlessly into the next, without any unnecessary pauses or delays. This synchronization of activities leads to increased productivity and output.
Imagine a manufacturing facility where scheduling is not given much importance. Workers are left waiting for materials, machines are left idle, and production lines are frequently interrupted. This chaotic environment not only hampers productivity but also leads to frustration among employees.
On the other hand, with effective scheduling, manufacturers can create a smooth and efficient workflow. They can allocate resources optimally, ensuring that each machine and worker is utilized to their full potential. By eliminating idle time and reducing setup times, manufacturers can achieve higher production rates and meet customer demands more effectively.
The Relationship Between Scheduling and Efficiency
Efficiency is the backbone of successful manufacturing operations. It is the ability to produce goods with minimum waste, maximum output, and optimal resource utilization. Effective scheduling is a key driver of efficiency in manufacturing.
By aligning production activities with available resources, manufacturers can avoid conflicts and optimize production sequences. This means that machines and workers are utilized in the most efficient manner, reducing unnecessary downtime and delays. The result is a streamlined workflow that minimizes lead times and maximizes output.
Furthermore, efficient scheduling enables manufacturers to identify and address bottlenecks in the production process. By analyzing the sequence of operations, manufacturers can identify areas where improvements can be made to enhance efficiency. This could involve rearranging the order of operations, investing in additional equipment, or implementing new technologies.
Ultimately, the relationship between scheduling and efficiency is a symbiotic one. Efficient scheduling leads to increased efficiency, while improved efficiency allows for better scheduling. This cycle of continuous improvement is essential for manufacturers to stay competitive in today's fast-paced and demanding market.
Strategies for Successful Production Planning
Implementing effective strategies for production planning is essential to achieve optimal results. Two key strategies that have proven successful are implementing Lean Manufacturing principles and balancing demand and supply.
When it comes to implementing Lean Manufacturing principles, there are several key practices that manufacturers can adopt. One such practice is Just-In-Time (JIT) inventory management. With JIT, manufacturers aim to have the right materials and components delivered at the exact time they are needed in the production process. This approach helps to minimize inventory holding costs and reduce waste associated with excess inventory.
In addition to JIT, continuous improvement is another essential aspect of Lean Manufacturing. By constantly seeking ways to improve processes, manufacturers can identify and eliminate inefficiencies, bottlenecks, and non-value-added activities. This continuous improvement mindset fosters a culture of innovation and drives productivity gains over time.
Standardized work procedures are also crucial in Lean Manufacturing. By establishing standardized processes and work instructions, manufacturers can ensure consistency and reduce variability in their production operations. This not only improves quality but also enhances efficiency and reduces the risk of errors or defects.
Implementing Lean Manufacturing Principles
Lean Manufacturing principles focus on eliminating waste and increasing efficiency throughout the production process. By implementing practices like Just-In-Time inventory management, continuous improvement, and standardized work procedures, manufacturers can streamline operations, reduce lead times, and increase overall productivity.
Another important strategy in production planning is balancing demand and supply. It is crucial for manufacturers to align production volumes with customer demand to avoid overproduction or stockouts. This requires careful analysis of market trends, customer preferences, and historical sales data.
Lead time is a critical factor to consider when balancing demand and supply. Manufacturers need to assess the time it takes to procure raw materials, produce finished goods, and deliver them to customers. By accurately estimating lead times, manufacturers can ensure that they have sufficient inventory to meet customer demand without excessive carrying costs.
Available resources and production capacity also play a significant role in balancing demand and supply. Manufacturers need to assess their equipment, manpower, and other resources to determine their production capabilities. By optimizing resource allocation and capacity utilization, manufacturers can avoid bottlenecks and maximize output.
Furthermore, technology can greatly assist in balancing demand and supply. Advanced forecasting and demand planning software can help manufacturers accurately predict future demand, enabling them to adjust production plans accordingly. This proactive approach ensures that manufacturers can meet customer expectations effectively and avoid costly disruptions in the supply chain.
Balancing Demand and Supply in Production Planning
An important strategy in production planning is balancing demand and supply. This involves aligning production volumes with customer demand while considering factors such as lead time, available resources, and production capacity. By closely monitoring customer demand and adjusting production plans accordingly, manufacturers can optimize their production processes and meet customer expectations effectively.
In conclusion, implementing Lean Manufacturing principles and balancing demand and supply are two key strategies for successful production planning. By embracing Lean Manufacturing practices such as JIT inventory management, continuous improvement, and standardized work procedures, manufacturers can streamline operations and increase productivity. Balancing demand and supply requires careful analysis of market trends, lead time, available resources, and production capacity. By leveraging technology and closely monitoring customer demand, manufacturers can optimize their production processes and ensure customer satisfaction.
Techniques for Effective Scheduling
In addition to production planning, effective scheduling techniques are essential to ensure smooth workflow and resource optimization. Leveraging technology and overcoming common scheduling challenges are key to achieving this.
When it comes to scheduling, there are various techniques that can be employed to streamline the process and maximize productivity. One such technique is known as "time blocking." This involves dividing the workday into specific time blocks dedicated to different tasks or activities. By allocating specific time slots for each task, employees can prioritize their work and focus on one thing at a time, leading to increased efficiency and reduced multitasking.
Another effective scheduling technique is known as "buffering." This involves intentionally leaving some extra time between tasks or appointments to account for unexpected delays or disruptions. By building in buffers, businesses can better handle unforeseen circumstances without causing major disruptions to the overall schedule. This technique not only helps maintain productivity but also reduces stress and improves employee morale.
The Role of Technology in Scheduling
Technology plays a vital role in modern scheduling techniques. Advanced scheduling software allows manufacturers to automate scheduling tasks, analyze complex production data, and generate optimized production sequences. By harnessing the power of technology, manufacturers can improve accuracy, increase agility, and adapt quickly to changing circumstances.
One of the key features of scheduling software is its ability to generate visual representations of the schedule, such as Gantt charts. These charts provide a clear overview of the entire project timeline, allowing managers to easily identify potential bottlenecks or conflicts. Additionally, scheduling software often comes with built-in collaboration tools, enabling different stakeholders to communicate and coordinate effectively, further enhancing the scheduling process.
Overcoming Common Scheduling Challenges
Although scheduling can be complex, there are strategies for overcoming common challenges. Effective communication and collaboration among different stakeholders is crucial to ensure that scheduling decisions consider all relevant factors. By involving all relevant parties, such as production managers, department heads, and team leaders, in the scheduling process, businesses can gain valuable insights and ensure that the schedule aligns with the overall goals and objectives.
Furthermore, proactive monitoring of bottlenecks and real-time adjustments to the schedule can help mitigate unexpected disruptions and maintain production efficiency. By regularly reviewing the schedule and identifying potential bottlenecks or areas of concern, businesses can take proactive measures to address these issues before they escalate. This could involve reallocating resources, adjusting task priorities, or even outsourcing certain tasks to external vendors to ensure smooth workflow and timely delivery.
Another common challenge in scheduling is managing conflicting priorities. In a dynamic business environment, conflicting priorities can arise, making it difficult to allocate resources and prioritize tasks effectively. To overcome this challenge, businesses can implement a prioritization framework that takes into account factors such as urgency, importance, and resource availability. By establishing clear criteria for prioritizing tasks, businesses can make informed decisions and ensure that the most critical tasks are given the necessary attention and resources.
In conclusion, effective scheduling techniques are crucial for optimizing workflow and resource utilization. By leveraging technology and implementing strategies to overcome common scheduling challenges, businesses can improve productivity, minimize disruptions, and achieve their production goals efficiently.
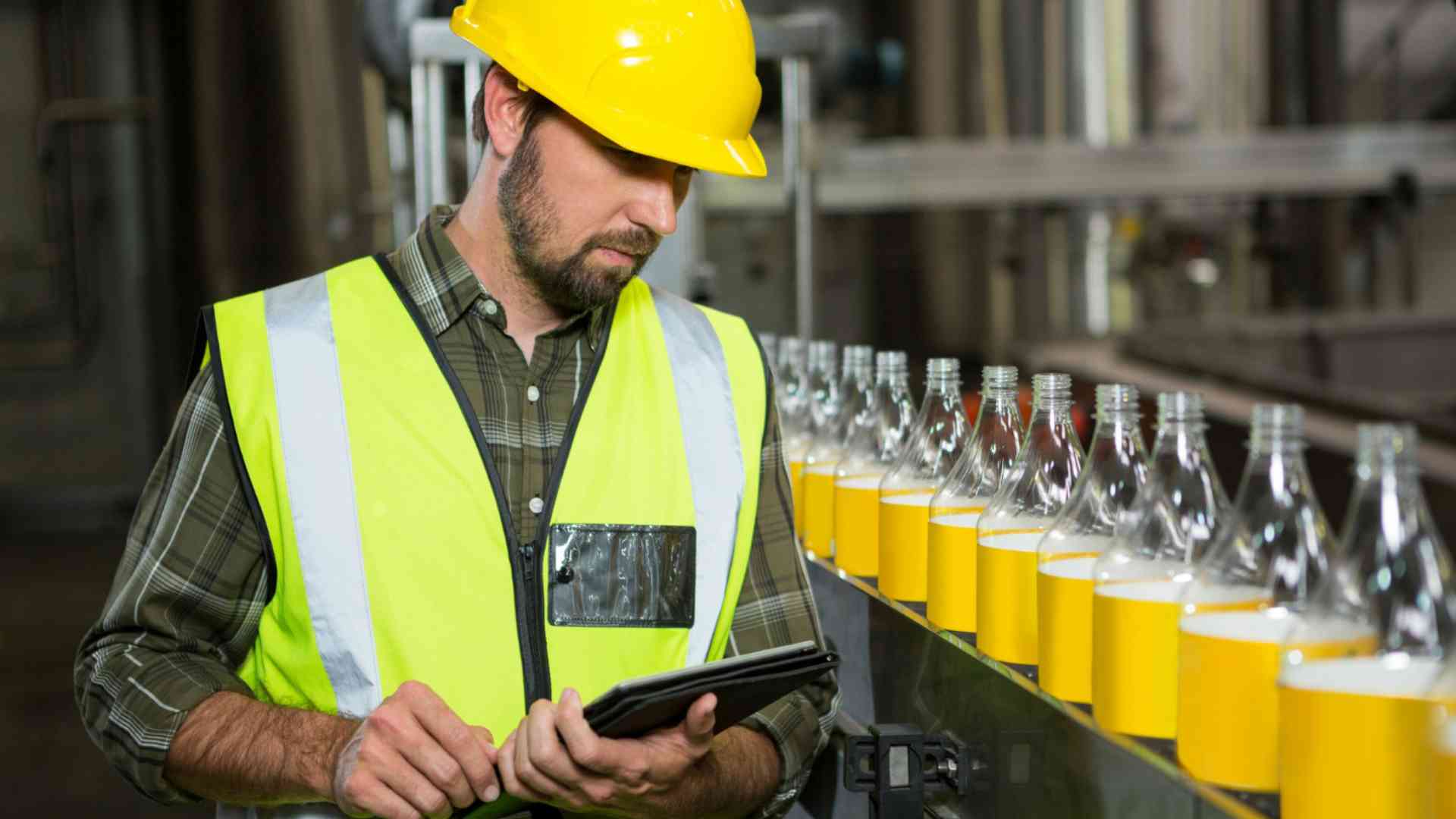
Integrating Production Planning and Scheduling
While production planning and scheduling are related concepts, integrating the two can bring numerous benefits to manufacturing operations.
Integrating production planning and scheduling is like bringing two puzzle pieces together to create a complete picture. It involves aligning the strategic decisions made during production planning with the tactical decisions made during scheduling. This integration creates a seamless flow of information and actions, resulting in a more efficient and effective manufacturing process.
The Benefits of Integrated Planning and Scheduling
By integrating production planning and scheduling, manufacturers can achieve better coordination between the two processes. This leads to enhanced visibility, improved accuracy, and streamlined workflows.
Imagine a manufacturing operation where production planning and scheduling are disconnected. The production planning team might create a detailed plan, but without integration, the scheduling team might not have access to that plan in real-time. This lack of visibility can lead to miscommunication, delays, and inefficiencies.
However, when production planning and scheduling are integrated, the entire manufacturing team can access and collaborate on a single, unified plan. This shared visibility allows for better communication and coordination, ensuring that everyone is working towards the same goals.
Furthermore, integration enables improved accuracy in forecasting and resource allocation. With real-time data synchronization between production planning and scheduling, manufacturers can make more informed decisions about inventory levels, machine utilization, and labor allocation. This accuracy helps minimize waste, reduce costs, and optimize overall production efficiency.
Streamlined workflows are another significant benefit of integrating production planning and scheduling. With integration, the handoff between planning and scheduling becomes seamless. The production plan seamlessly flows into the scheduling process, eliminating the need for manual data entry or rework. This streamlined workflow saves time and reduces the risk of errors, allowing manufacturers to operate more efficiently.
Steps to Achieve Integrated Production Planning and Scheduling
Implementing an integrated software solution that combines production planning and scheduling functionalities is often a crucial step. This allows for seamless data transfer and real-time synchronization between the two processes, maximizing the benefits of a digital production line.
However, software alone is not enough. Successful integration also requires collaboration and alignment between the production planning and scheduling teams. Clear communication channels and shared goals are essential to ensure that both teams are working towards a common objective.
Additionally, training and education play a vital role in achieving integration. Both the teams need to understand the benefits and intricacies of integration. Training programs can help employees develop the necessary skills and knowledge to effectively utilize the integrated solution and collaborate seamlessly.
Regular monitoring and evaluation are also crucial to maintaining the effectiveness of integrated production planning and scheduling. Continuous improvement efforts, such as analyzing performance metrics and soliciting feedback from employees, can help identify areas for optimization and ensure that the integration remains aligned with the evolving needs of the manufacturing operation.
The Future of Production Planning and Scheduling
The manufacturing industry is constantly evolving, and production planning and scheduling are no exception. They are integral to the success of manufacturing operations, and are continuously evolving due to emerging technologies.
Manufacturers can optimize their operations, increase productivity, and stay ahead in an ever-changing market by understanding the intricacies of production planning and scheduling, implementing effective strategies, integrating these processes, and embracing future trends.
The Impact of Industry 4.0 on Production Planning
Industry 4.0, characterized by the integration of cyber-physical systems and the Internet of Things (IoT), promises improved effectiveness and flexibility in production planning. Real-time data collection and analysis enable manufacturers to make data-driven decisions, optimize production processes, and respond proactively. This leads to increased agility, reduced costs, and enhanced customer satisfaction.
With the advent of Industry 4.0, production planning is no longer a static process. Instead, it becomes a dynamic and interconnected system where machines, devices, and systems continuously exchange data with each other. This connectivity allows for real-time monitoring and control of production processes, enabling manufacturers to identify and address issues as they arise or even before they arise. By leveraging the power of IoT, manufacturers can achieve seamless integration between different stages of production, resulting in reduced lead times.
Furthermore, Industry 4.0 opens up new possibilities for predictive maintenance. By continuously monitoring the condition of machines and equipment, manufacturers can detect potential failures before they occur, minimizing unplanned downtime. This predictive approach not only improves overall equipment effectiveness but also optimizes production planning by ensuring that resources are available when needed.
In conclusion, the future of production planning and scheduling is shaped by emerging trends such as Industry 4.0 and automation. By embracing these technologies and leveraging the power of real-time data analysis, manufacturers can achieve higher efficiency, increased flexibility, and improved customer satisfaction. As the manufacturing industry continues to evolve, it is crucial for manufacturers to stay informed about these trends and adapt their production planning and scheduling processes accordingly.