Production planning is a crucial aspect of manufacturing operations. In order to streamline processes and optimize efficiency, manufacturers rely on advanced software solutions. With the rapid advancements in technology, it becomes essential for manufacturers to stay updated with the latest production planning software options in the market. In this article, we will explore the 10 best production planning software for manufacturing in 2024.
SAP S/4HANA
.jpeg)
SAP S/4HANA, often regarded as one of the leading production planning software solutions in the market, is SAP's next-generation Enterprise Resource Planning (ERP) suite designed specifically to work with SAP’s in-memory database, SAP HANA. It was launched in 2015 to succeed SAP R/3 and SAP ERP and represents a significant shift from traditional database-dependent ERP systems to leveraging the speed and efficiency of in-memory computing.
SAP S/4HANA is particularly well-suited for complex manufacturing scenarios requiring detailed production planning. It offers flexibility in deployment options, including on-premise, cloud, or hybrid models, to meet various IT infrastructure and data governance requirements.
Core Functionalities in Production Planning
1. Advanced Planning and Scheduling (APS)
APS in SAP S/4HANA takes traditional MRP (Material Requirements Planning) a step further by considering constraints such as machine capacity, labor, and material availability in real-time. It enables planners to perform detailed scheduling, which is critical for optimizing manufacturing processes and throughput.
2. Material Requirements Planning (MRP)
SAP S/4HANA enhances MRP functionality by executing planning runs more quickly due to the in-memory technology. It supports both MRP on the fly, for immediate planning results, and the traditional MRP, which can be scheduled to run at regular intervals.
3. Capacity Planning
The system provides tools to assess and manage production capacities, ensuring that resources are used effectively. This involves analysis of work center capacities, machine capabilities, and labor allocations against the requirements specified by the production schedule.
4. Inventory Management
SAP S/4HANA offers real-time inventory management, which helps in maintaining optimal inventory levels. The tight integration with other modules like Material Management (MM) and Sales and Distribution (SD) provides end-to-end visibility of the inventory, reducing stockouts and overstock situations.
5. Integration with Manufacturing Execution Systems (MES)
The seamless integration with MES allows for the execution of manufacturing operations, data collection, and real-time monitoring, ensuring the production plan aligns closely with actual shop-floor activities.
Oracle NetSuite
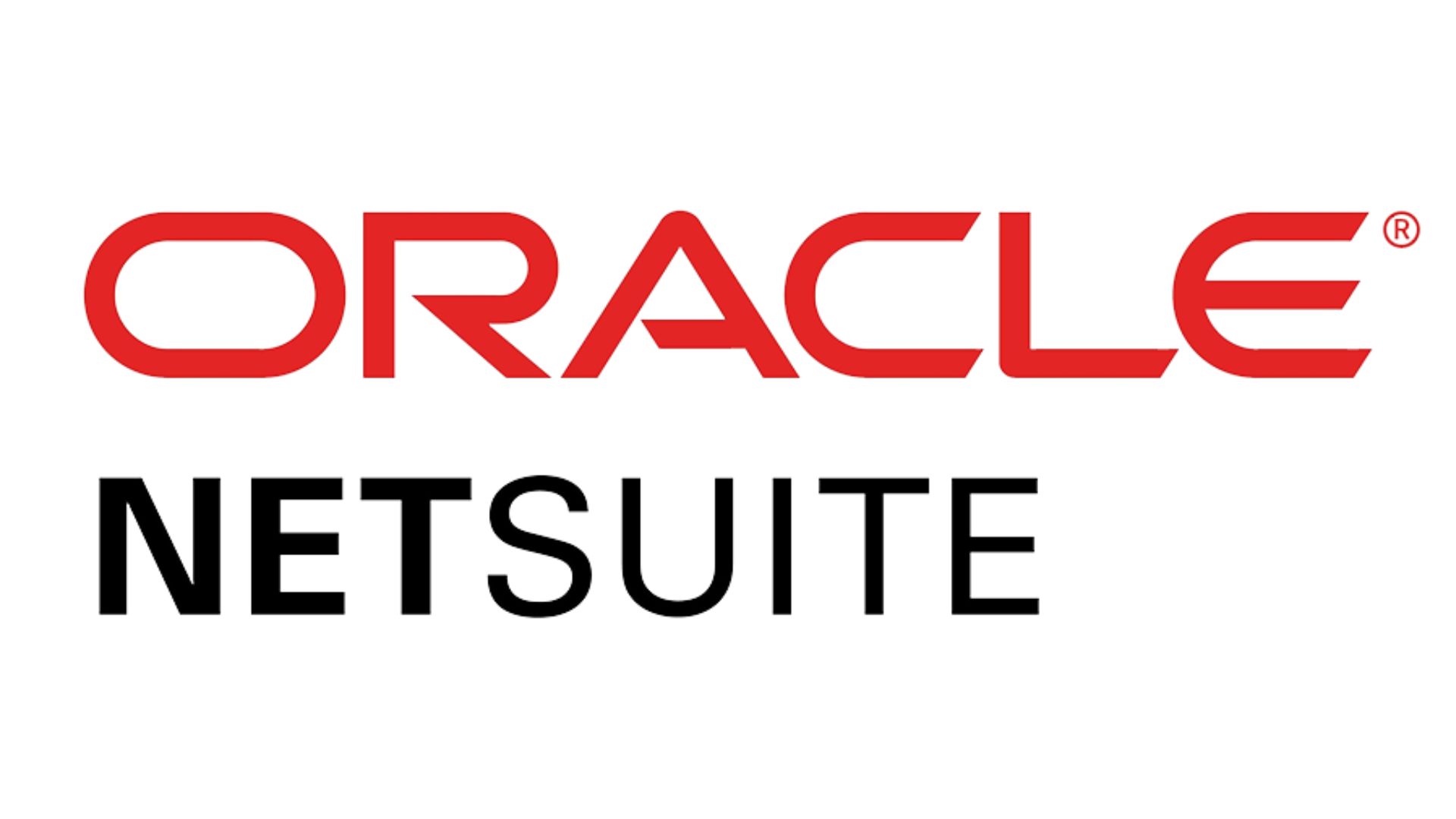
Oracle NetSuite is a comprehensive cloud-based Enterprise Resource Planning (ERP) suite that includes a wide range of functionalities specifically tailored for business management. Within its extensive suite of applications, NetSuite provides robust capabilities for production planning, offering businesses an end-to-end solution to manage their manufacturing operations efficiently. It is particularly well-regarded for its scalability and flexibility, making it a popular choice for fast-growing small to medium businesses, as well as established enterprises looking for a cloud-based solution.
NetSuite production planning tools are particularly beneficial for process and discrete manufacturers. Being a SaaS (Software as a Service) solution, NetSuite's deployment is exclusively cloud-based, offering a straightforward subscription model that is regularly updated with new features and capabilities.
Core Functionalities in Production Planning
1. Demand Planning
NetSuite's demand planning capabilities enable businesses to predict required inventory levels based on historical data, sales forecasts, average trends, and seasonal fluctuations. This ensures that companies can optimize their inventory levels, improve cash flow, and reduce the holding costs associated with excess inventory.
2. Work Order Management
NetSuite provides a centralized system to manage work orders for the production process. This allows for the efficient creation, release, update, and monitoring of work orders throughout the production cycle, improving the management of the manufacturing process from work order issuance to work completion.
3. Bill of Materials (BOM)
NetSuite supports comprehensive BOM management, which includes detailed definitions for simple and complex products, along with routing and resource requirements. This ensures that all materials needed for production are accurately documented, managed, and tracked.
4. Routing and Scheduling
It allows businesses to define the detailed steps necessary in the manufacturing process and associate them with specific work centers. NetSuite's scheduling capabilities consider both the resource capacity and the calendar of each work center, helping businesses to optimize production schedules.
5. Real-Time Visibility
With its cloud-based platform, Oracle NetSuite provides real-time visibility into all aspects of production planning. This includes current work order statuses, inventory levels, and detailed production reports, allowing for proactive decision-making.
Grid
.jpeg)
Work on Grid is a comprehensive production planning software that combines scheduling, resource management, and advanced analytics to help manufacturers achieve optimal production efficiency. The software's powerful optimization algorithms consider various constraints, such as resource availability, demand variability, and production costs, to create realistic and feasible production plans.
Core Functionalities in Production Planning
1. Process Control
- Workflow Management: Capabilities that enable manufacturers to define and automate production processes, including routing, scheduling, and quality checks. This helps ensure that production processes are consistent and repeatable, reducing errors and need for manual intervention.
- Production Planning: Empowers manufacturers to create and manage production plans, including scheduling, batch management, and material tracking. This helps ensure that production runs according to plan, with minimal delays or disruptions.
- Real-Time Monitoring: Manufacturers can optimize their production runs based on real-time data. This helps in immediate decision-making and reducing downtime.
2. Shop Floor Control
- Task Assignment: Grid provides features for assigning manufacturing tasks to team members and monitoring their progress.
- Shop Floor App: An additional mobile application for workers to update task statuses, ensuring real-time tracking.
3. Cloud-Native Solution
- Anywhere Access: Since it's cloud-based, manufacturers can access their data and the platform from anywhere, ensuring flexibility and real-time decision-making. The cloud architecture allows businesses to easily scale up or down based on their requirements.
- Operator Interface: Provides an intuitive operator interface that allows production staff to easily interact with the system. This includes visual dashboards, alerts, and notifications that provide real-time information about production status, equipment performance, and quality metrics.
4. Quality Management
- Inspection & Testing: Build quality inspection and testing apps that help in reducing defects and ensuring product consistency. This includes tracking quality metrics, managing defect rates, and implementing corrective actions as needed.
- Material Tracking: Allows manufacturers to track materials from receipt through production and shipping. This includes tracking material lots, serial numbers, and expiration dates, ensuring that materials are properly traced and accounted for.
Plex Smart Manufacturing Platform
.jpeg)
Plex is designed to support manufacturers in various industries, including automotive, aerospace, food and beverage, and industrial manufacturing. As a cloud-native solution, it provides real-time connectivity and data across the entire manufacturing operation, from the shop floor to the top floor. Plex is particularly recognized for its strength in managing the complexity of manufacturing operations, ensuring quality compliance, and enabling data-driven decision-making.
Core Functionalities in Production Planning
1. Production Scheduling
Plex offers advanced production scheduling features that allow manufacturers to optimize their production runs. The scheduling tools consider machine availability, labor, material requirements, and maintenance schedules to maximize efficiency and throughput.
2. Material Requirements Planning (MRP)
The platform's MRP capabilities help manufacturers plan and manage inventory effectively, ensuring that the right materials are available at the right time to meet production demands.
3. Real-Time Shop Floor Control
Plex provides real-time control and visibility into shop floor activities. It tracks the production process, machine performance, and operator activities, enabling immediate responses to production issues.
4. Quality Management
With integrated quality management functionality, Plex ensures that manufacturing processes adhere to quality standards. This includes features for in-process checks, statistical process control, and compliance with industry-specific quality standards.
5. Traceability and Compliance
Plex excels in product traceability, which is vital for industries like food and beverage or automotive. It tracks and documents every step in the manufacturing process, which is essential for compliance and quality assurance.
ProShop
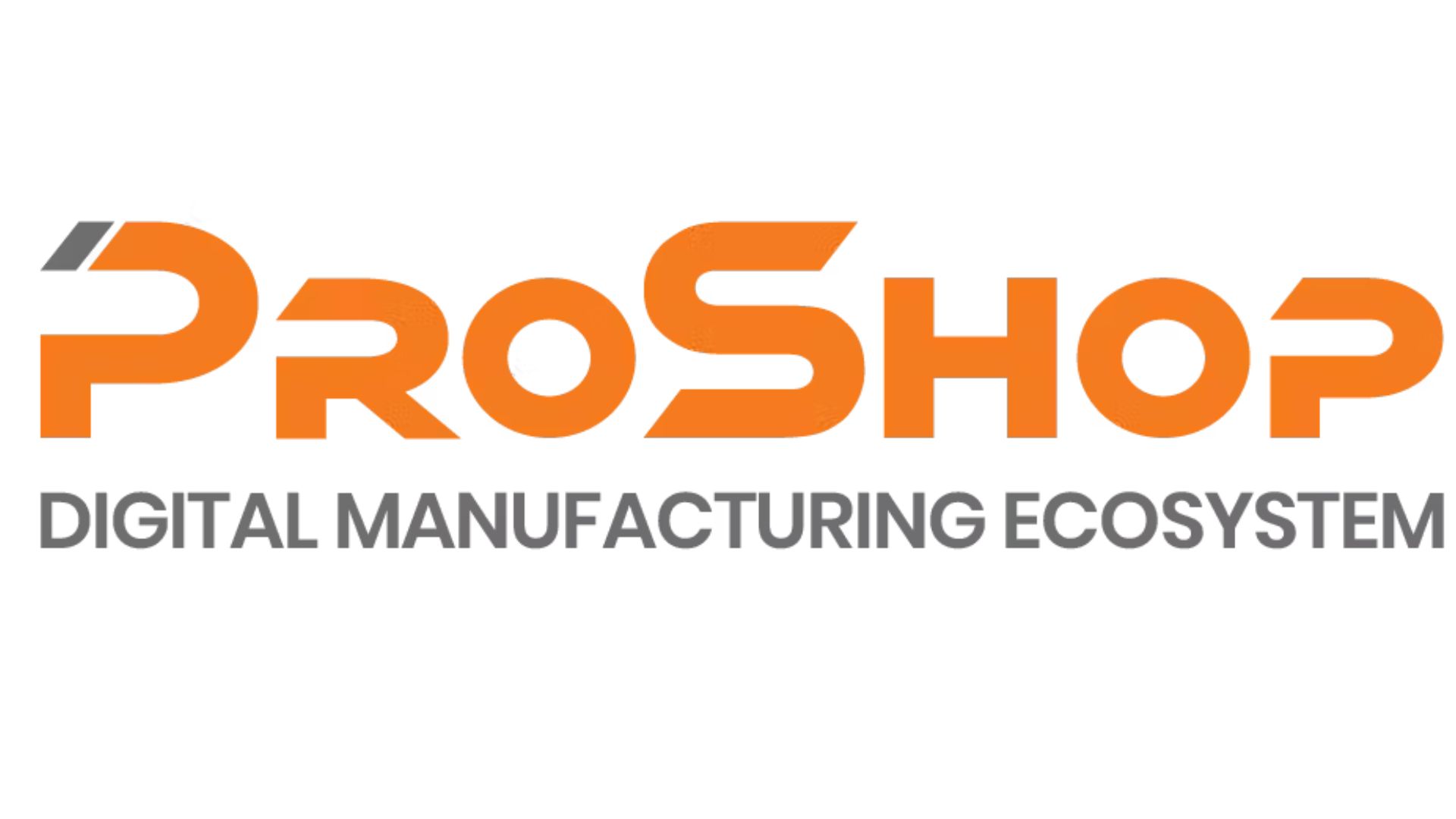
Developed by Adion Systems, ProShop describes itself as a Digital Manufacturing Ecosystem, aiming to be more than just a traditional ERP system. It's a comprehensive web-based and shop management system designed for small to medium-sized manufacturers, particularly those operating within the precision manufacturing industry. It combines various functionalities that are critical for efficient production planning and management, including ERP (Enterprise Resource Planning), MES (Manufacturing Execution System), and QMS (Quality Management System).
While ProShop is suitable for various manufacturing sectors, it is especially beneficial for precision manufacturing companies and those with complex, highly regulated, or quality-focused manufacturing processes. ProShop is a web-based system, offering cloud deployment. This makes it accessible from anywhere, supporting businesses that have remote teams or multiple locations.
Core Functionalities in Production Planning
1. Work Orders and Workflows
ProShop's system allows for the creation of detailed work orders, defining all aspects of manufacturing processes, from material procurement to final inspection. Its workflow management is robust, providing step-by-step instructions and ensuring all processes are followed accurately.
2. Production Scheduling
The software offers dynamic production scheduling tools, allowing planners to see real-time views of their shop floor capacity and to plan work based on machine availability, labor, and current workload.
3. Detailed Routing
Manufacturing operations can be routed in meticulous detail within ProShop, ensuring that every step of the manufacturing process is accounted for. This includes machine setup times, operation sequences, and quality checkpoints.
4. Machine and Tool Integration
ProShop can integrate with shop floor machinery and tooling, providing direct data feeds into the system for real-time tracking and management of the manufacturing process.
5. Inventory and Material Tracking
The system includes comprehensive inventory management tools that track materials from receipt through to finished goods. It provides detailed materials traceability, which is essential for industries with strict compliance requirements.
Simio
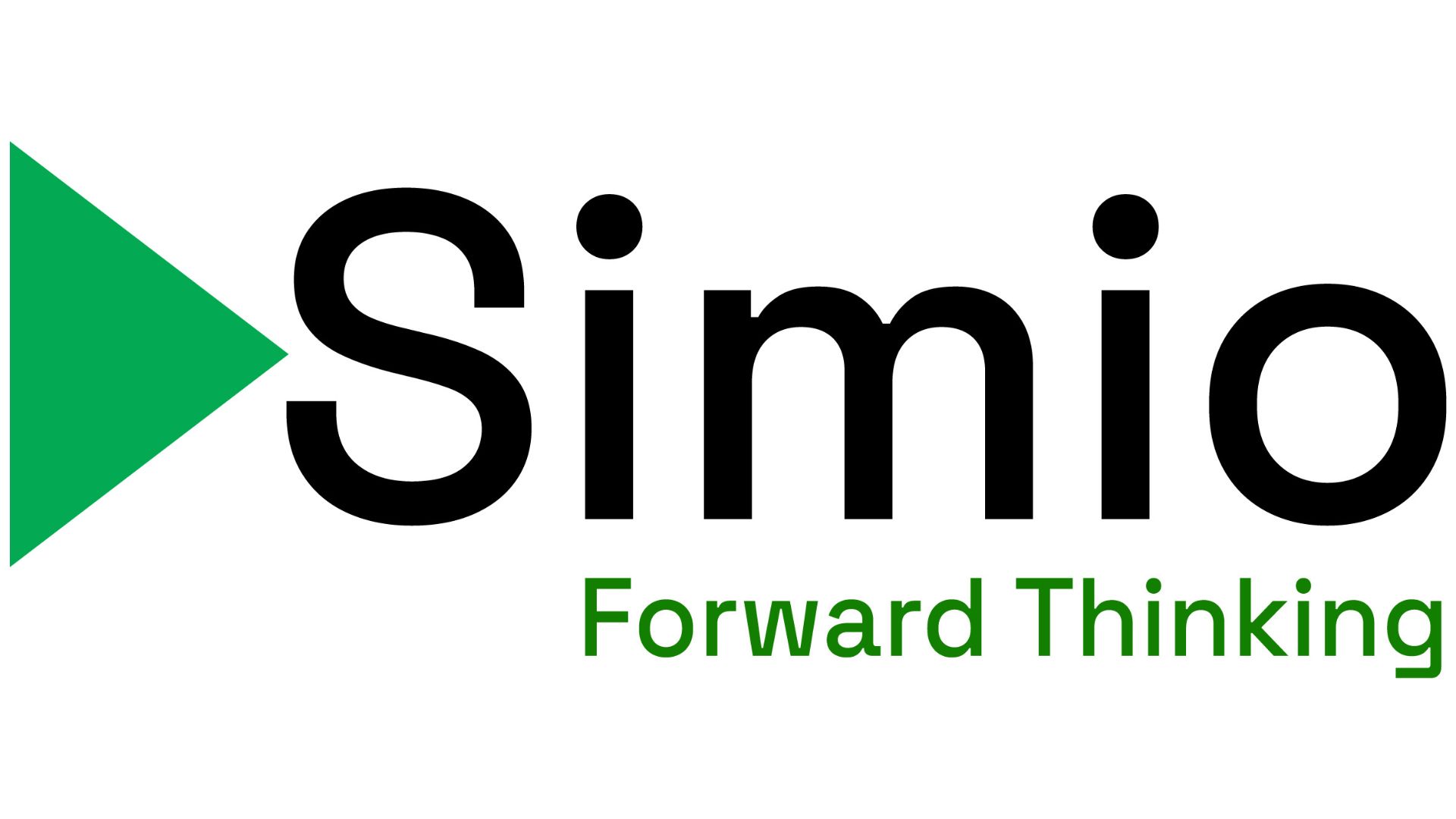
Simio is a state-of-the-art simulation software that offers advanced production planning and scheduling capabilities. Unlike traditional ERP systems, Simio specializes in using simulation modeling to predict and improve the performance of manufacturing systems before they are built or altered. It is particularly valuable for complex and dynamic manufacturing environments where variability and uncertainty make it challenging to plan production effectively using conventional methods. Simio's software is distinguished by its ability to incorporate the stochastic nature of manufacturing environments — variability in processing times, machine breakdowns, and unpredictable supply chain disruptions — into its planning and scheduling models.
Simio is versatile and can be applied across various industries that require detailed planning and risk analysis in their production processes. It is particularly well-suited for aerospace, automotive, heavy machinery, and any complex manufacturing environments. Simio provides flexible deployment options, including both cloud-based and on-premises solutions, catering to different IT infrastructure preferences and data handling policies.
Core Functionalities in Production Planning
1. Predictive Simulation
Simio allows users to build 3D simulation models of their production facilities. These models can be used to predict the impact of new production plans, changes in layout, or adjustments to the manufacturing process under uncertain conditions.
2. Scheduling with Risk Analysis
Simio's scheduling software is risk-aware, meaning it can account for uncertainties and provide a risk analysis on proposed schedules. This feature enables manufacturers to not only create schedules that optimize resource utilization but also understand the probabilities of potential delays or issues.
3. Interactive Scheduling
Users can interact with the Simio scheduling model, adjusting parameters, and immediately seeing the impact of those changes. This interactivity provides planners with the flexibility to test various scenarios and find the best solutions in real-time.
4. Scenario Analysis
With Simio, manufacturers can compare different "what-if" scenarios, such as changes in demand, machine downtimes, or shifts in resource availability. This capability helps in making informed decisions based on comparative outcomes and performance metrics.
5. Real-Time Data Integration
Simio can integrate with existing data systems to pull in real-time data, which allows the simulation and schedules to reflect the current state of the manufacturing environment accurately.
MasterControl Manufacturing Excellence
.jpeg)
MasterControl Manufacturing Excellence is a solution designed to bridge the gap between performance and quality in manufacturing operations, specifically tailored for regulated industries. It’s part of the MasterControl suite, which is known for its robust quality management systems (QMS). As a top production planning software, MasterControl Manufacturing Excellence integrates the principles of QMS directly into the production process, thus ensuring compliance and efficiency are not mutually exclusive goals. It's designed to help manufacturers increase their agility, reduce product cycle times, and get to market faster while ensuring compliance with regulatory standards like FDA regulations and ISO quality standards.
The software is specifically tailored for life sciences and other regulated industries that require meticulous record-keeping and adherence to strict manufacturing standards. MasterControl offers cloud-based solutions that provide flexibility and scalability to growing businesses. This also allows for lower upfront costs compared to on-premises deployment.
Core Functionalities in Production Planning
1. Electronic Batch Records (EBR)
The software’s EBR functionality replaces paper-based records, significantly reducing errors associated with manual data entry. It streamlines the review and approval processes, which in turn accelerates production cycles.
2. Device History Records (DHR)
For medical device manufacturers, MasterControl automates the creation of DHRs, ensuring that each step of the manufacturing process is properly documented and compliant with regulatory requirements.
3. Production Process Adherence
It ensures that all production processes adhere strictly to predetermined workflows, thereby minimizing deviations and non-conformance.
4. Integrated Quality Management
MasterControl integrates quality processes such as corrective and preventive actions (CAPAs), change control, and training directly into the production environment, thereby facilitating a seamless quality management process.
5. Data Integrity and Traceability
The solution provides a high level of traceability and data integrity, which is essential for manufacturers that need to comply with regulations like FDA 21 CFR Part 11 and similar global standards.
DELMIAWorks
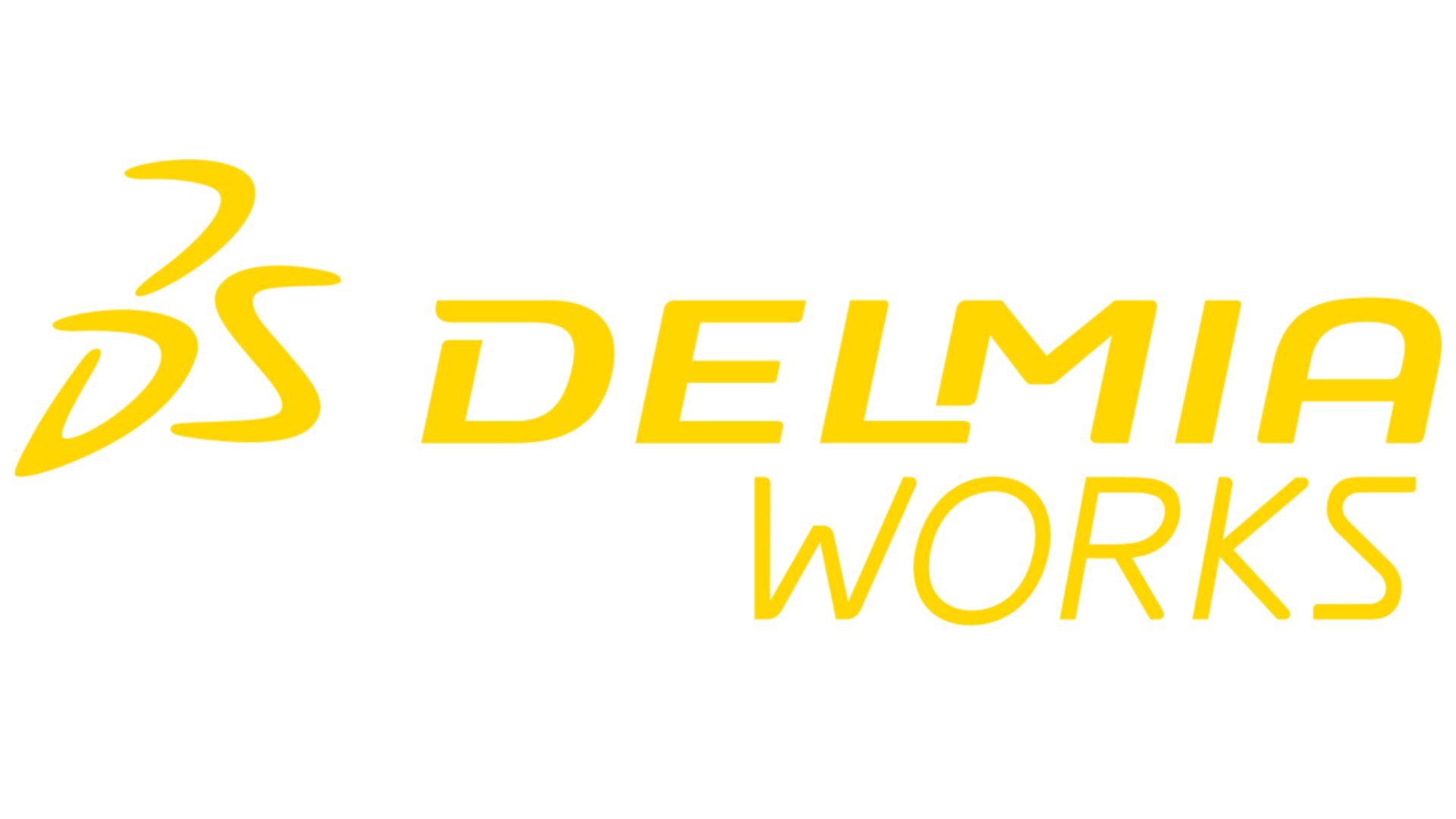
DELMIA, part of Dassault Systèmes' brand suite, which acquired IQMS and its ERP solutions, offers an extensive suite of software applications for manufacturing and operations planning. Specifically, the DELMIAworks (formerly known as IQMS ERP) is a comprehensive enterprise resource planning system that has been designed to meet the unique needs of manufacturing companies. As a production planning software, DELMIAworks provides tools for manufacturers to plan, schedule, track, and manage their operations efficiently.
DELMIAworks is particularly strong in discrete manufacturing sectors and is well-suited to manufacturers who operate in a make-to-order, make-to-stock, or mixed-mode production environment. Dassault Systèmes offers DELMIAworks as both an on-premises solution and a cloud-based option, providing flexibility depending on the manufacturer's infrastructure and preferences.
Core Functionalities in Production Planning
1. Real-Time Monitoring and Scheduling
DELMIAworks features real-time production monitoring, which allows for immediate visibility into machine status, production rates, and shop floor activities. Its advanced scheduling tools can handle complex, multi-step production processes and optimize the use of resources.
2. Process and Quality Control
With built-in process monitoring and quality management, DELMIAworks ensures that production operations meet the stringent standards required by various industries, especially those that are highly regulated.
3. Inventory Management and Control
Inventory management within DELMIAworks is fully integrated into the production planning process, providing accurate and real-time inventory levels, reducing carrying costs, and minimizing the risk of stockouts or overstock.
4. Detailed Reporting and Analytics
The software comes equipped with robust reporting tools and dashboards that offer insights into production efficiency, cost analysis, and performance metrics, supporting data-driven decision-making.
5. Supply Chain Management
It extends beyond the walls of the manufacturing plant to offer complete supply chain visibility and management, which is critical for just-in-time manufacturing environments.
Epicor Kinetic
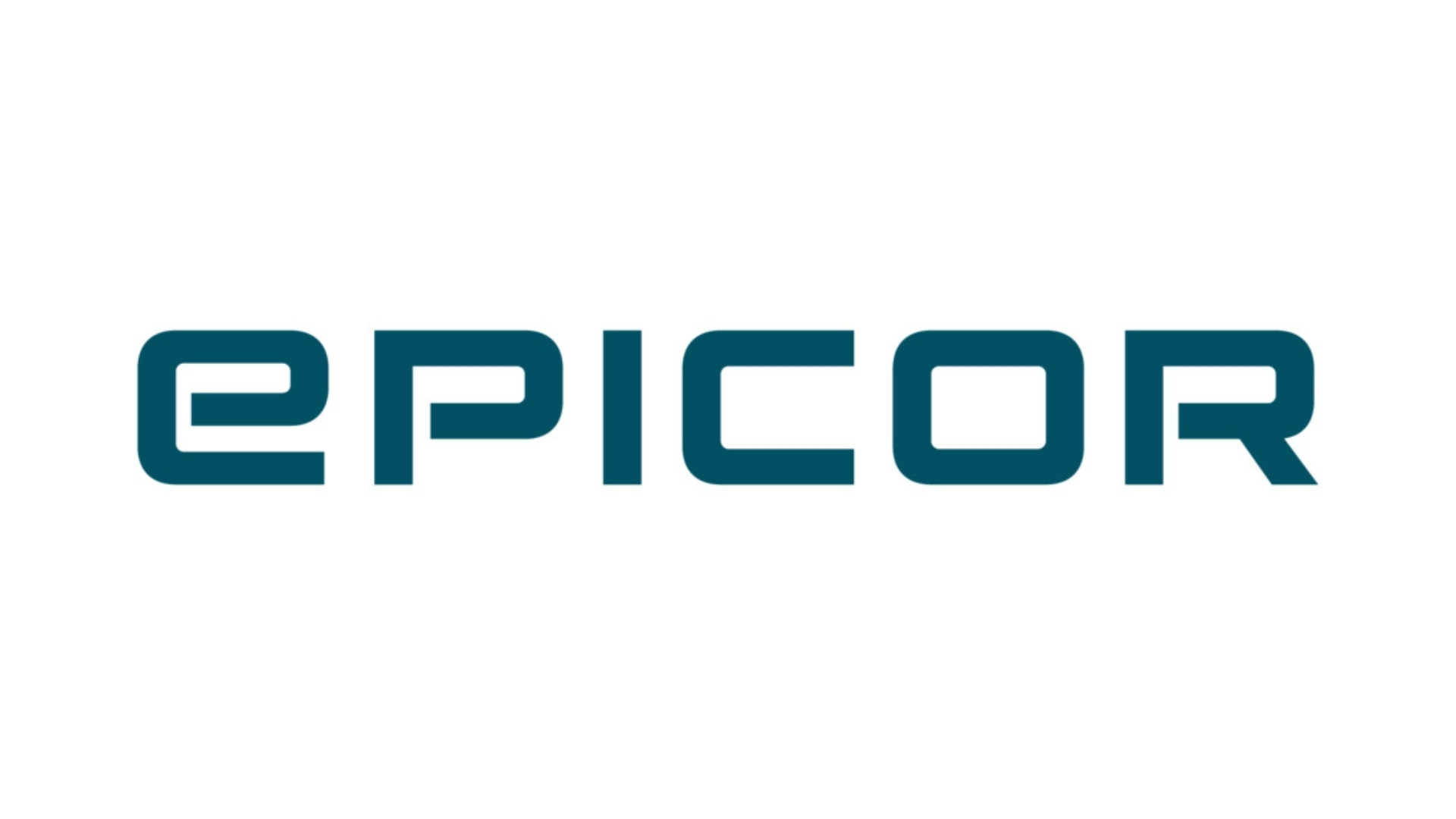
Epicor Kinetic is built specifically for manufacturers, blending deep functionality with a user-friendly interface. It's a modern ERP solution that provides real-time, end-to-end visibility into manufacturing operations. The platform is adaptable to various manufacturing modes, including make-to-order (MTO), make-to-stock (MTS), engineer-to-order (ETO), and more, making it suitable for a wide range of industries.
Core Functionalities in Production Planning
1. Advanced Planning and Scheduling (APS)
Epicor Kinetic features an Advanced Planning and Scheduling system that helps manufacturers balance supply and demand by considering both material and production constraints. This tool enables more accurate and efficient scheduling, reducing lead times and increasing throughput.
2. Material Requirements Planning (MRP)
The MRP functionality within Epicor Kinetic helps in planning, scheduling, and managing the manufacturing process from raw materials to finished goods. It ensures that materials and components are available for production while maintaining the lowest possible material and product levels in stock.
3. Real-Time Data and Analytics
Epicor Kinetic offers real-time visibility into production operations, allowing manufacturers to make informed decisions based on the latest data. This includes monitoring machine performance, work-in-progress status, and overall production efficiency.
4. Quality Management
Quality management is integrated into the workflow, helping businesses ensure product quality and compliance with industry standards and regulations.
5. Inventory Management
Epicor Kinetic provides comprehensive tools for managing inventory, including tracking of raw materials, work-in-progress items, and finished goods.
SYSPRO
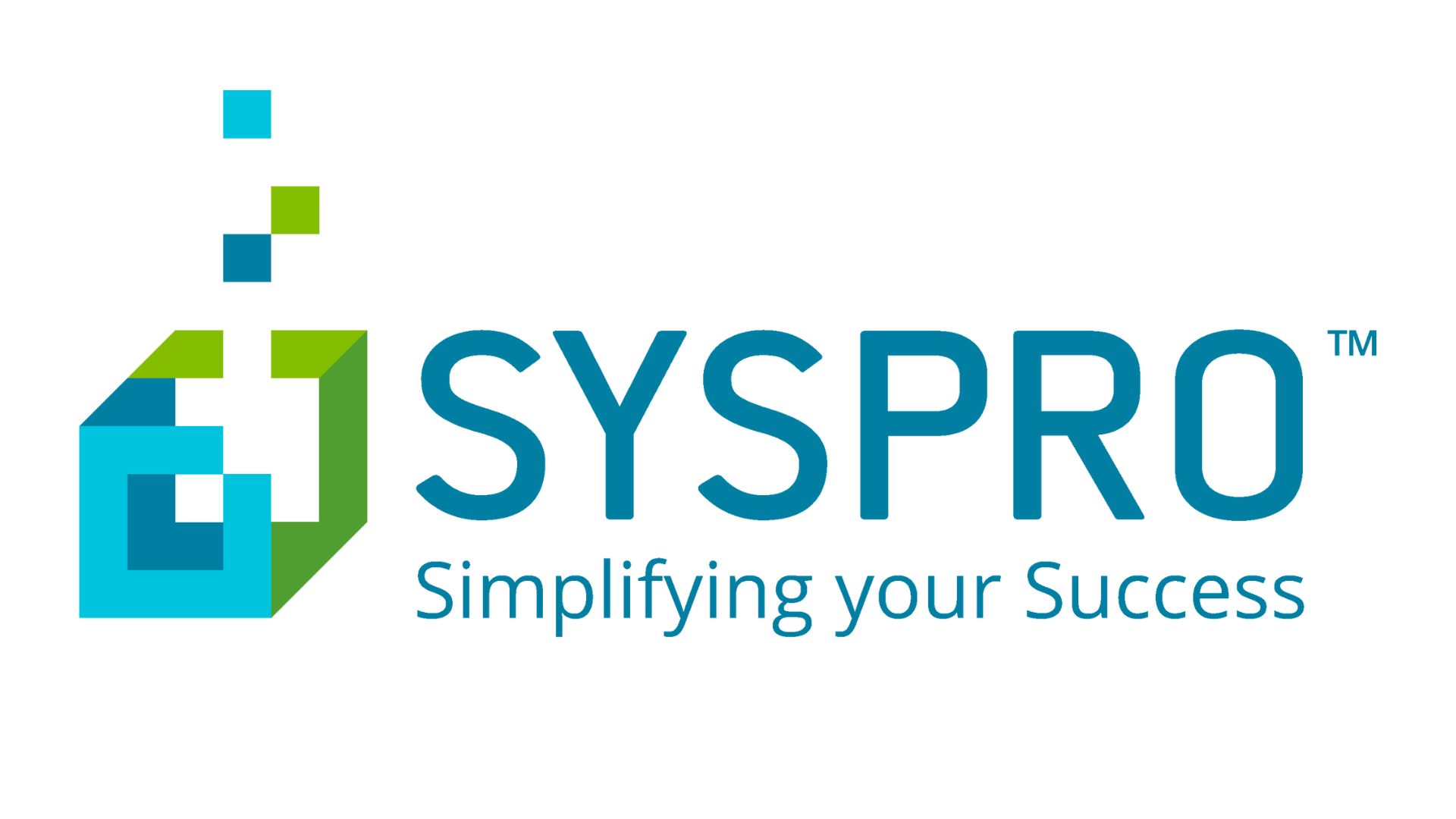
SYSPRO's ERP solution offers a wide range of features tailored for various manufacturing modes, including make-to-stock, make-to-order, configure-to-order, and engineer-to-order. It is designed to provide manufacturers with the flexibility and capabilities needed to manage industry-specific challenges and take advantage of market opportunities. The software emphasizes real-time data access, extensive reporting capabilities, and a customizable interface to enhance usability and decision-making.
Core Functionalities in Production Planning
1. Demand Planning
SYSPRO incorporates forecasting and planning tools that allow businesses to anticipate customer demand and adjust production schedules accordingly. This helps in maintaining optimal inventory levels and improving customer service.
2. Production Scheduling
It offers detailed scheduling capabilities, including finite and infinite capacity scheduling, ensuring that businesses can effectively allocate resources, manage lead times, and deliver orders on schedule.
3. Advanced Planning and Scheduling (APS)
SYSPRO’s APS module enhances production planning by providing tools to support complex, multi-step manufacturing processes, and optimizing the use of machinery, labor, and materials.
4. Material Requirements Planning (MRP)
The MRP functionality ensures that all materials required for production are available when needed, helping to prevent bottlenecks and minimize excess inventory.
5. Shop Floor Control
SYSPRO provides real-time insights into shop floor operations, allowing businesses to track the progress of jobs, monitor machine utilization, and manage labor effectively.