Utilities across verticals: water, electricity, solar, have to manage a large number of diverse assets installed across numerous locations and stored in multiple warehouses. Grid, our utility data management solution is designed to simplify the complexities involved in managing inventories. This is achieved through tailored workflows that enhance visibility and control over multiple assets, advanced tracking capabilities and much more. In this blog, we will consider two scenarios for utilities: smart metering and water infrastructure projects, and how Grid can be leveraged to improve asset utilization and mitigate associated risks.
Use case: Smart meter installation project
During smart meter installation projects, smart metering companies need to maintain transparency into inventory stocks and avoid situations that may result in operational slowdown. Grid’s comprehensive operational data management platform can be used by utilities (smart metering companies in this context) for project lifecycle management involving various processes. These include surveys, real-time reporting, O&M and inventory management.
During the installation phase, managing the inventory is a critical process. This involves management of both serialized (fixed) and non-serialized (variable) assets. Moreover, there can be multiple contractors, categories of smart meter equipment and warehouses which need to be tracked, opening up possibilities of misplacement, pilferage or damages.
In the initial stages of the project, Grid’s no-code solution can be used for surveying, with the data collected being leveraged to create an inventory management workflow. This allows the easy tracking of every single smart meter equipment that will be procured and stored, drilled down to individual serial numbers.
How Grid was used for inventory management during smart metering installation
One of our smart metering customers was able to ensure that every single material was available on-time, and allowed them to prevent instances of cost overrun or pilferage. Let’s explore step-by-step how Grid was used to streamline the procurement and storage of new meters.
Step 1: With the data collected during the survey, a plan or a framework was drawn up for the inventory and installation process. This framework was drawn up with timelines, deliverables and a clear indication of which parties were responsible for each step of the project.
Step 2: Next, the ‘Meter Stock-in’ entry form is used to identify the amount and details of meters for the warehouse. The form captured details such as location of the warehouse, meter category, meter price and meter serial number. This step ensured every critical data associated with individual meters are logged in for data accuracy.
Step 3: During the meter installation phase, third party installers have to be issued smart meters from warehouses. The ‘Meter Stock-in’ worksheet can also be used for this process, with form capturing all the necessary meter details along with meter issue date and name of the project. In this way, smart metering companies ensure that no smart meters are misplaced or lost while issuing them to third-party installers.
Step 4: During the installation process, there are instances of meters getting lost or being damaged during transportation. Grid can also be used to create a worksheet to capture details regarding ‘Missing/Damaged Meters’. With capabilities to upload pictures in the form itself, third party installers or field operators can attach images as proof for damaged meters and update the status of meters within the worksheet. Once the meter is confirmed and marked defective, it is automatically omitted from the workflow data.
Step 5: Users set up a dashboard for the live monitoring of inventory during the project. They leveraged Grid’s reporting features to get an overview of total number of stocked meters, along with associated data like number of meters that are yet to be issued or the number of installed meters. The transparency achieved via Grid enabled the smart metering company to always stay one step ahead in inventory and planning, ensuring availability of stocks throughout.
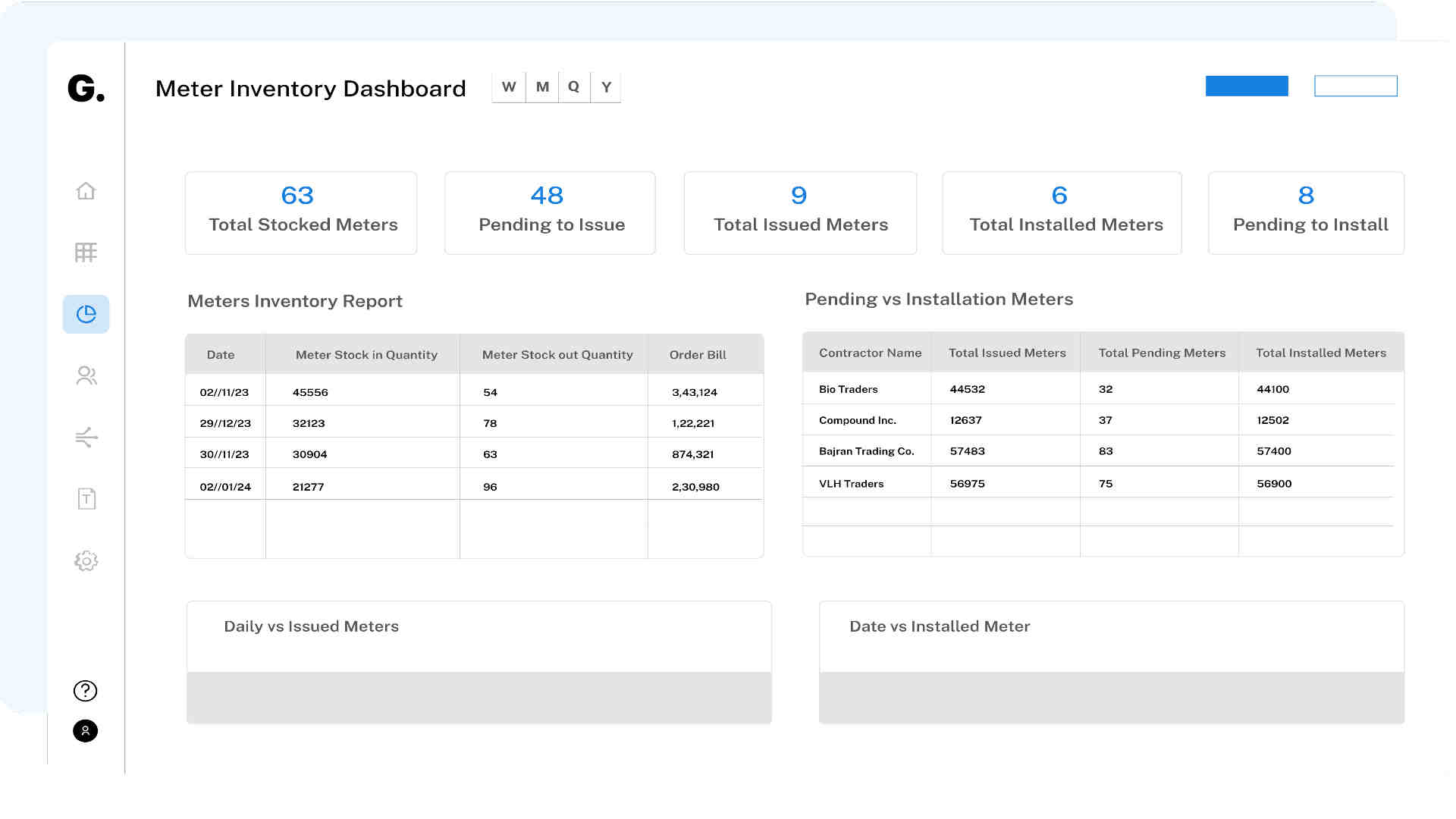
To minimize delays and improve resource allocation during inventory shortages, QR codes were also created to scan the items in-and-out of the warehouse, improving transparency into stock levels at all times.
This automated approach to inventory management ensures that there are no operational disruptions from surveys to the installation phase. Grid’s custom worksheets can also be set up to track KPIs such as installation per day against targets, inventory discrepancies, reconciliation, etc.
Use Case: Water Infrastructure Projects for EPC companies
EPC companies associated with infrastructure development can be often involved in projects which involve building a complex network of water distribution systems. In such scenarios, Grid can be used as a Project Management which enables the tracking of data across multiple regions. This also helps in timely reporting with regards to aspects of material management and procurement optimization in such projects, ensuring the project completion status is always met.
How Grid was used for material management in water infrastructure projects
We will explore how Grid’s no-code solution was deployed as a project management solution to optimize procurement activities for timely availability of materials by a water utility enterprise. This section will also highlight how Grid can be implemented to create material management sheets that efficiently tracks material use across project locations.
Step 1: Grid’s platform was used by teams to create multiple sheet trackers; streamlining processes like purchase requisition, purchase order creation and inventory aging.
Step 2: Users were able to track information for each vendor and the materials procured from them, with detailed view into PO no, material code, vendor code, order quantity, etc. They could now easily view the order quantity that is yet to be delivered at each warehouse location, and from order placement to final delivery.
Step 3: Grid’s customizable worksheets also highlighted the inventory status of various storage locations that are part of the water infrastructure project. The status view can also be segmented along the lines of various districts that come under the project and stock quantity.
Step 4: The water utility company also created a workflow for hindrance tracking with regards to optimizing their inventory levels. A workflow dashboard was designed to highlight on-site hindrances such as lack of inventory, detailing the particular location that has been impacted. This enabled management to prioritize issues and act in a swift manner to ensure there are no hindrances in their ongoing operations.
Step 5: Teams can now get a comprehensive breakdown of their asset management with regards to inventory and its specific challenges, like hindrance tracking and inventory aging. For instance, users set up Grid’s dashboard to get detailed insights into open and closed hindrance tickets. The dashboarding feature also provided line item details for inventory aging such as the name of the supplier, material code and the aging bucket they fall in.
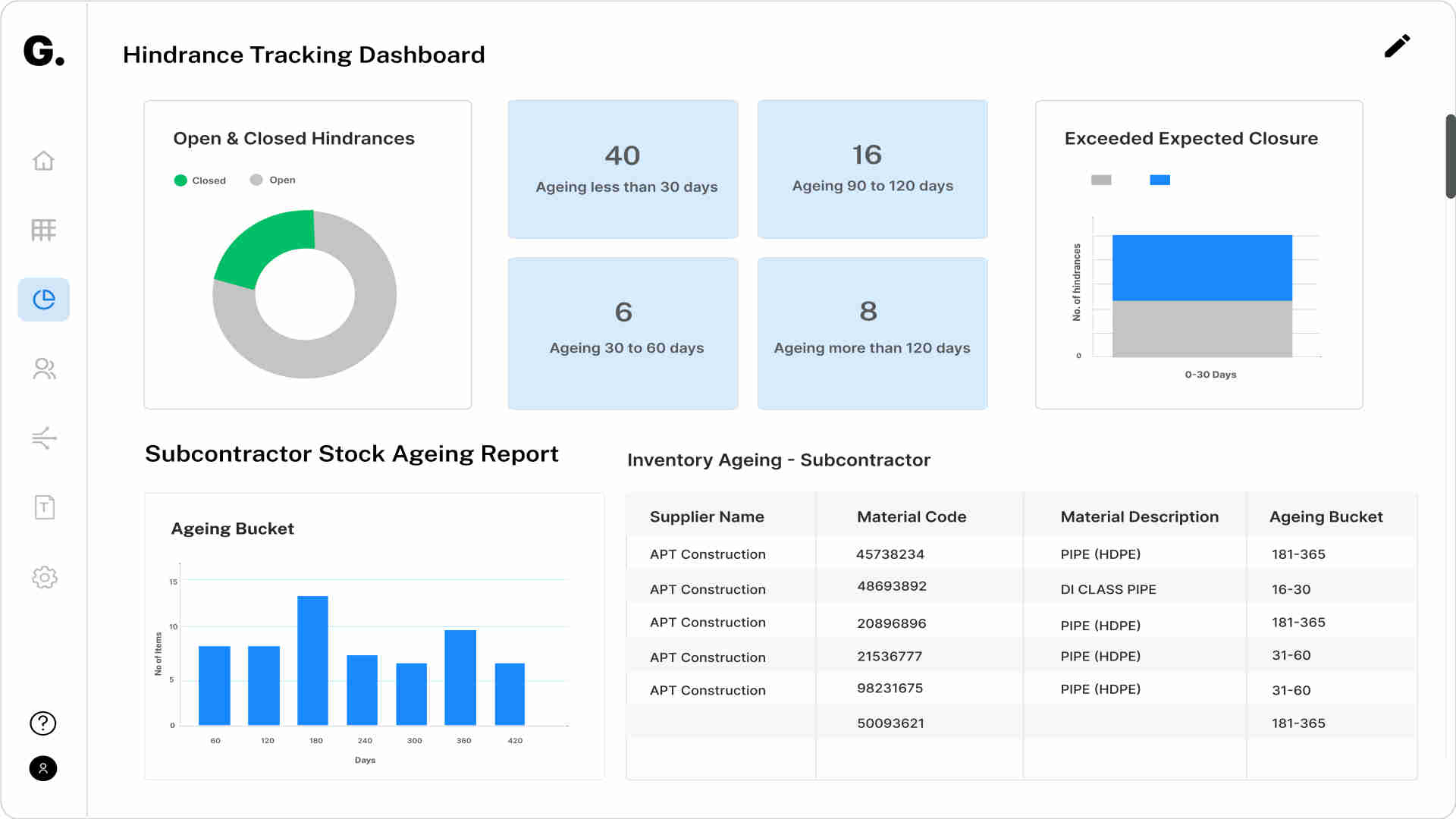
This end-to-end transparency into inventory management allows the effortless tracking of inventory levels, guarantee timely availability of materials, eliminate pilferage and minimize risk of stock-outs.
Conclusion
When assets are not tracked properly and emergencies arise, the entire supply chain can be subjected to interruptions or operational disruptions. Moreover, utility projects span over a large period of time, from months to even years, with multiple field workers allocated for various tasks. This means that workers need to be equipped with the right tools and parts at all times. Utilities also need to have an end-to-end control over their inventory operations, so that the equipment is available whenever required, helping them lower costs and reduce delays.
Schedule a demo today or speak with one of our Grid experts to understand how a no-code solution transforms your inventory management approach from reactive to proactive. With Grid by your side, stay ahead of operational disruptions, ensure optimal inventory levels at every touchpoint, no matter the location or duration.